Chiang Mai city produces over 300 tonnes of garbage per day, managed by the municipality, which while working to turn a bulk of the waste into energy, still uses the practice of landfills to rid our city of waste. This practice has dire consequences to the environment, due to pollutants. Chiang Mai University, however, is leading the charge for waste management by managing its 15 tonnes per day of waste with its own zero-waste biomass system.
Assistant Professor Dr. Pruk Aggarangsi Director Energy Research and Development Institute - Nakornping
“About 90% of Thailand’s waste goes into landfills,” said Assistant Professor Dr. Pruk Aggarangsi, Director of the Energy Research and Development Institute – Nakornping (ERDI-CMU). “Unlike countries such as Singapore, we have always had a lot of land, and this was the common and easy method of disposal. But it is like having a nuclear power plant, it is so dangerous for the environment. Following rains, these landfills become swamps of putrid waste and if there are heavy metals in the waste, then the damage can be untold. What is critical is that this has become the norm.”
15 tonnes of garbage per day delivered to plant
Chiang Mai University has been on a path of innovative sustainability for some while now, and its aggressive strategy of using innovation for environmental and energy purposes is now being harnessed, by working with experts in the field of bio gas and energy, resulting in the foundation of the ERDI-CMU. The purpose is not to simply turn 15 tonnes of waste per day into zero waste, but also to instill in its students and faculty, new practices and awareness of waste disposal.
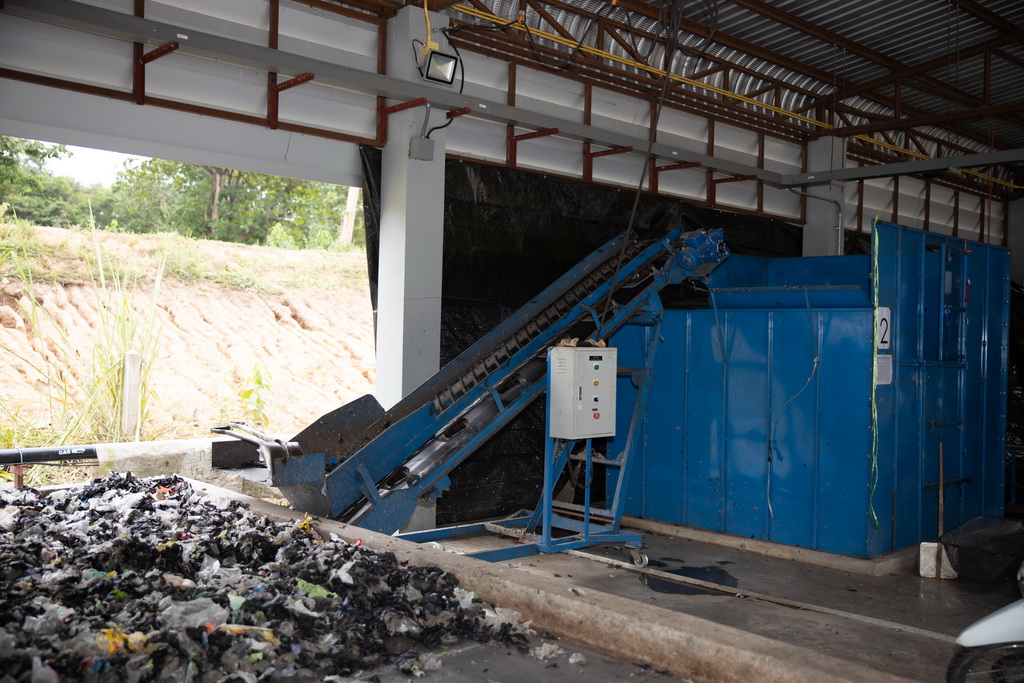
Mechanical sorting system to reduce labour
In order to instill a zero waste mindset, the university now has students and staff set up garbage bins and dispose of waste into six types: 1. General/wet waste (blue bin), 2.Recycle/salable/dry waste (yellow bin), 3.Wet food waste (food hall bins), 4. Dangerous/medical waste (red bags), 5. Biomass waste such as leaves and branches (biomass factory), and 6. Construction waste/foam (municipality).
“We can barely manage to tie up garbage bags at home, as they smell so much,” explained Assistant Professor Dr. Pruk. “In one day the bin starts stinking. But if people get into the habit of separating their waste, then it’s just a small amount which goes off, the rest can sit there for days, requiring far less effort. We at the university feel as though it’s our duty to do it first, even if it costs lots of money. We need to lead by example. Our D Day was in 2017, when we first opened our factory. While some of our waste does get sent to the landfill, most of it doesn’t; our aim is to reduce the buried waste to under 5%, and in time to zero. Each year we have 8,000 graduates who have the potential to create 8,000 communities out there. If we can instill the right practices in them then it is exponential.”
“Zero waste is not sending the garbage off to another district to become their problem,” he continued. “It is about solving the problem right here. When you see that the garbage which is separated suddenly has value, and is resalable, then it is attractive to many people.
The university still relies on the municipality to collect the garbage it disposes, but then it is all brought to the university’s biomass plant, where machinery then sorts it out, whether to make fertiliser, to resell, or to recycle. Technology is used in garbage sorting, in fermenting for biogas and in the production of bio-methane gas used to create electricity for the university’s usage. This energy is currently used to fuel the electric trams which are used as the on-campus free transport. The plastic is turned into refuse-derived fuel (RDF), following the university’s formula and methodology, which is mixed with asphalt to build and fix the university’s roads. As to the biomass waste, it is used to turn into activated charcoal and fuel pellets and the fat residue is used to make biodiesel, etc.
“Our factory first separates waste,” explained Assistant Professor Dr. Pruk, “then we turn that waste into something usable such as making fuel, asphalt or making bricks for building roads—we are still burying this waste, but it is now biodegradable. Next year we think we will be ready to sell these bricks on the market. When we hire a company to come and construct our roads, we simply work with them by offering them the use of our waste products. Then there is the masses of plastic or glass items which we clean thoroughly and wait for the price to be right so that we can sell them. As to the wet waste, we quickly ferment it into methane gas, a natural process which yields energy. There is nothing new or innovative about much of this, in fact, His Majesty King Rama IX was turning fat into biodiesel thirty years ago. If we do it right, then the community won’t have any smells or unsightly waste to complain about; even better money made can be used to better the community.”
Bio methane-propelled transportation shuttling students between campuses (CBG)
The biomass plant currently processes 900 cubic square metres of bio gas per day which is then turned into 5,200 kilowatts per hour per year. It also produces 18,000 kilograms per year of CBG as well as reducing the number of buried and burned waste by 4,050 tonnes per year and the number of buried wet waste by 5000 tonnes per year. A further 125 tonnes per year of fat residue is also saved from burial.
Chiang Mai University’s biomass plant, which had a budget of 80 million baht from the government to build, is located on the university’s Mae Hia campus, the first of its kind to complete the waste management cycle, in the country. This is a pilot project which has proven its worth and which can be replicated nationwide.
Bio mass plant for a sustainable future
“This biomass plant is all about the environment and energy,” Assistant Professor Dr. Pruk continued. “Chiang Mai University has shown that we are responsible for ourselves and for society, now the challenge is getting this knowledge out into real world practice in society at large. No one wants to live near a power plant, but once it’s all been properly separated—plastic, wood or materials, rubber—and the rest becomes salable, then it’s not objectionable. Thailand’s communities have long fought against nearby power plants and landfills, but if our model is followed, then it shouldn’t be a problem anymore. I do admit that this plant has cost a lot of money, and if we were to build it now it would cost in excess of 100 million baht. But how to you measure the cost to the environment?”